Advanced Welding WPS: Tailoring Requirements for Facility Jobs
Unlocking the Power of Welding WPS: Methods for Performance and Safety And Security in Manufacture
In the world of manufacture, Welding Procedure Specs (WPS) stand as the backbone of welding operations, dictating the essential steps for accomplishing both efficiency and security in the manufacture process. Understanding the complexities of WPS is vital to harnessing its complete potential, yet several organizations have a hard time to open the true power that lies within these files (welding WPS). By diving into the approaches that maximize welding WPS, a world of enhanced performance and heightened safety awaits those ready to discover the nuances of this crucial facet of manufacture

Relevance of Welding WPS
The importance of Welding Procedure Specifications (WPS) in the fabrication market can not be overemphasized. WPS work as an essential roadmap that lays out the necessary actions to ensure welds are performed continually and appropriately. By defining necessary specifications such as welding procedures, materials, joint styles, preheat temperatures, interpass temperatures, filler metals, and post-weld warmth treatment demands, WPS provide a standardized technique to welding that boosts efficiency, quality, and safety in fabrication processes.
Adherence to WPS aids in achieving uniformity in weld top quality, minimizing the possibility of issues or structural failures. This standardization likewise facilitates conformity with sector policies and codes, ensuring that fabricated frameworks fulfill the called for safety and security standards. In addition, WPS documents allows welders to reproduce effective welding procedures, leading to constant results throughout various tasks.
Basically, the precise advancement and rigorous adherence to Welding Procedure Requirements are paramount for promoting the integrity of welded frameworks, securing against possible dangers, and supporting the credibility of construction companies for supplying top notch product or services.
Key Aspects of Welding WPS
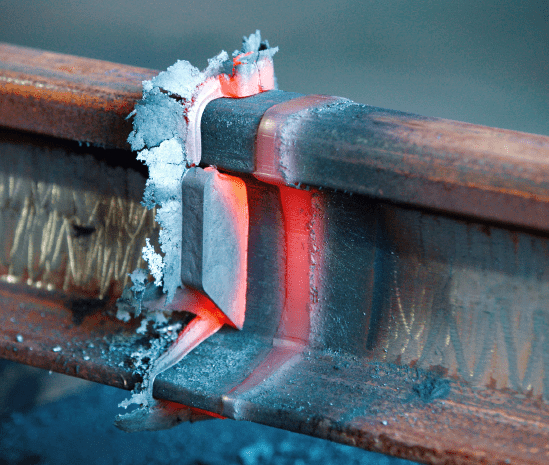
Enhancing Effectiveness With WPS
When maximizing welding procedures, leveraging the crucial elements laid out in Welding Treatment Requirements (WPS) ends up being important for enhancing processes and maximizing performance. One means to enhance efficiency with WPS is by very carefully selecting the ideal welding parameters. By sticking to the particular guidelines supplied in the WPS, welders can make sure that the welding tools is set up correctly, causing consistent and top quality welds. Furthermore, following the pre-approved welding series described in the WPS can dramatically minimize the time invested on each weld, eventually raising total productivity.
Furthermore, proper training and accreditation of welders in understanding and applying WPS can even more improve performance. Making certain that all team members are skilled index in translating and performing the WPS properly can remodel and decrease mistakes, conserving both time and sources. Regularly evaluating and upgrading the WPS to include any type of lessons discovered or technical improvements can likewise add to performance enhancements in welding procedures. By embracing the guidelines stated in the WPS like it and constantly looking for ways to maximize procedures, makers can accomplish higher efficiency levels and superior end outcomes.
Ensuring Safety And Security in Construction
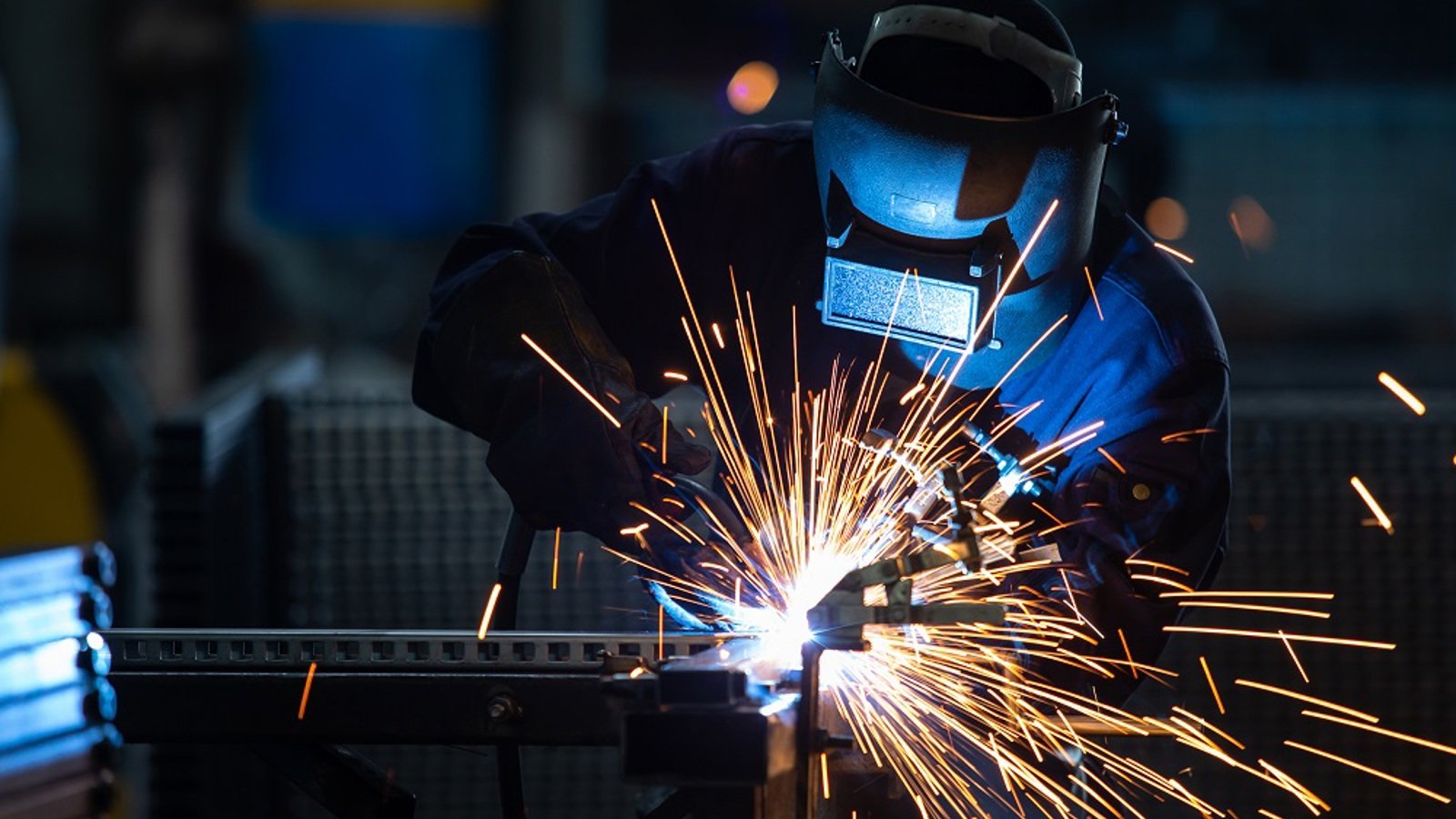
Security methods in construction play a pivotal duty in securing workers and maximizing operational procedures. Guaranteeing security in fabrication involves a complex approach that incorporates different elements of the welding process. One fundamental aspect is the stipulation of individual protective equipment (PPE) tailored to the specific dangers existing in the construction environment. Welders have to be geared up with suitable gear such as safety helmets, handwear covers, and protective apparel to minimize dangers connected with welding activities.
Moreover, adherence to appropriate ventilation and fume extraction systems is crucial in maintaining a healthy and balanced workplace. Welding fumes contain hazardous compounds that, if inhaled, can position serious health threats. Implementing reliable ventilation procedures helps to decrease exposure to these unsafe fumes, promoting breathing health among workers.
Regular devices upkeep and assessments are likewise vital for guaranteeing safety in fabrication. Malfunctioning machinery can cause accidents and injuries, emphasizing the significance of regular checks and timely fixings. By focusing on precaution and fostering a imp source culture of awareness, fabrication facilities can produce a safe and productive job setting for their workers.
Applying WPS Ideal Practices
To boost operational performance and guarantee high quality results in construction processes, including Welding Procedure Specification (WPS) best practices is extremely important. Choosing the appropriate welding process, filler product, and preheat temperature specified in the WPS is critical for attaining the preferred weld quality. Making sure that qualified welders with the needed accreditations carry out the welding procedures according to the WPS guidelines is necessary for uniformity and integrity.
Final Thought
In final thought, welding WPS plays a crucial duty in guaranteeing effectiveness and security in fabrication processes. By adhering to these methods, services can unlock the full potential of welding WPS in their construction procedures.
In the realm of fabrication, Welding Treatment Requirements (WPS) stand as the backbone of welding procedures, dictating the required steps for attaining both efficiency and security in the manufacture procedure. By specifying important criteria such as welding procedures, products, joint designs, preheat temperatures, interpass temperatures, filler steels, and post-weld warmth treatment needs, WPS supply a standardized strategy to welding that enhances effectiveness, high quality, and safety in fabrication procedures.
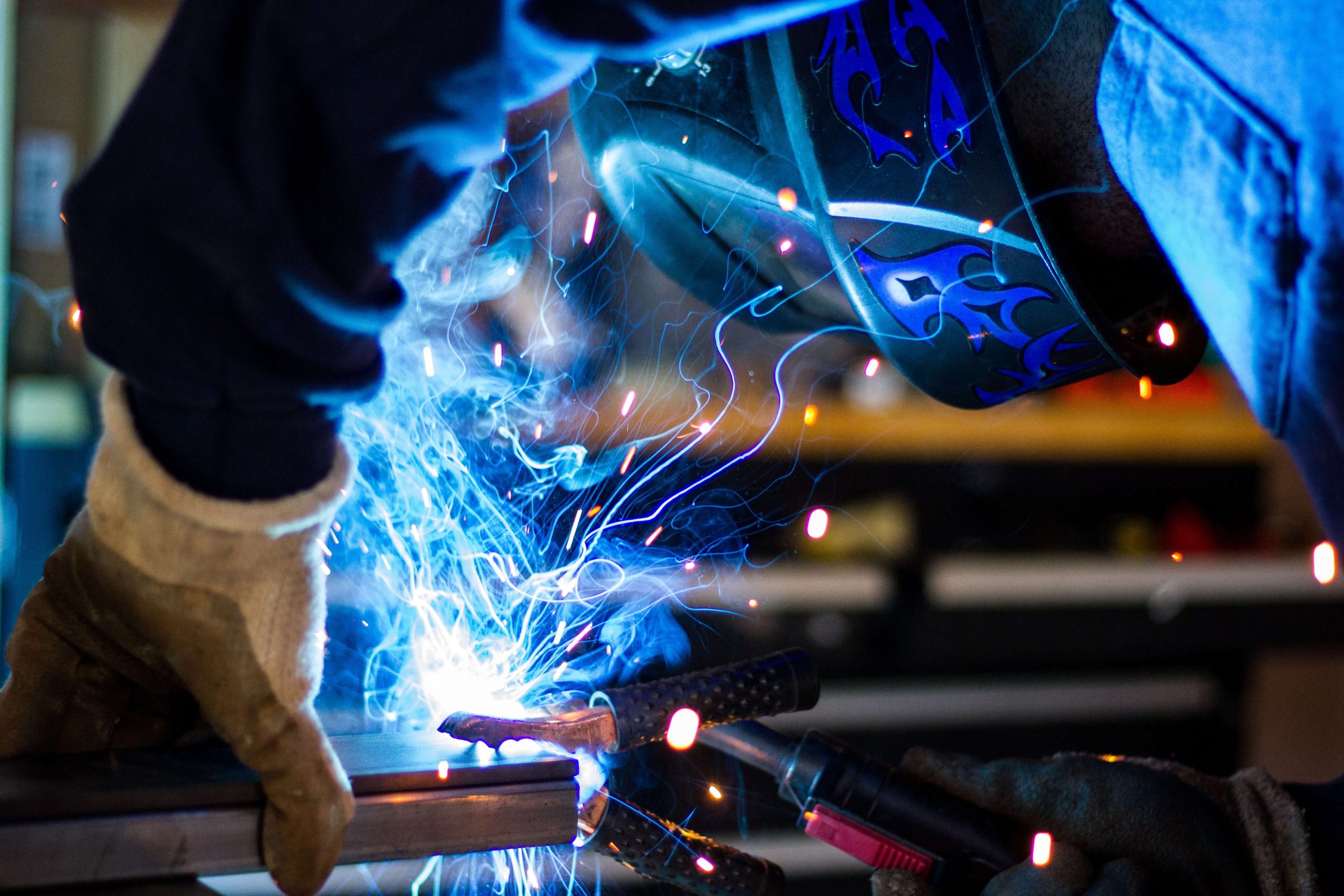
When maximizing welding procedures, leveraging the crucial elements described in Welding Procedure Specifications (WPS) ends up being necessary for improving procedures and optimizing performance. (welding WPS)